SustainabilitySocietyQuality management and customer satisfaction
We are aiming to be a company trusted by customers and are striving to provide products and
services that satisfy customer requirements.
We also want our business partners to grow
alongside us through activities based on our partnerships.
Enhancing customer satisfaction
Working daily to deliver inspiration to customers
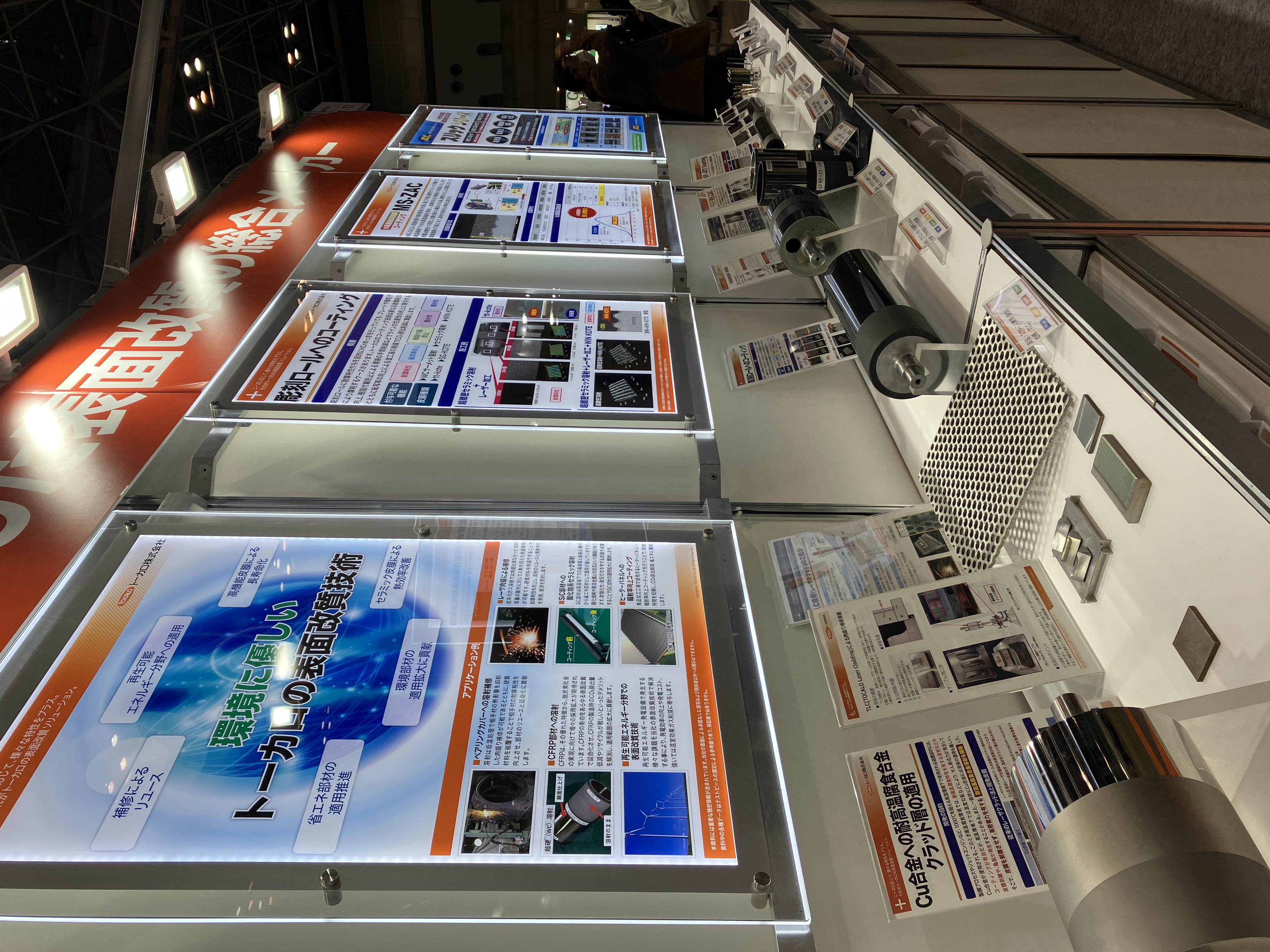
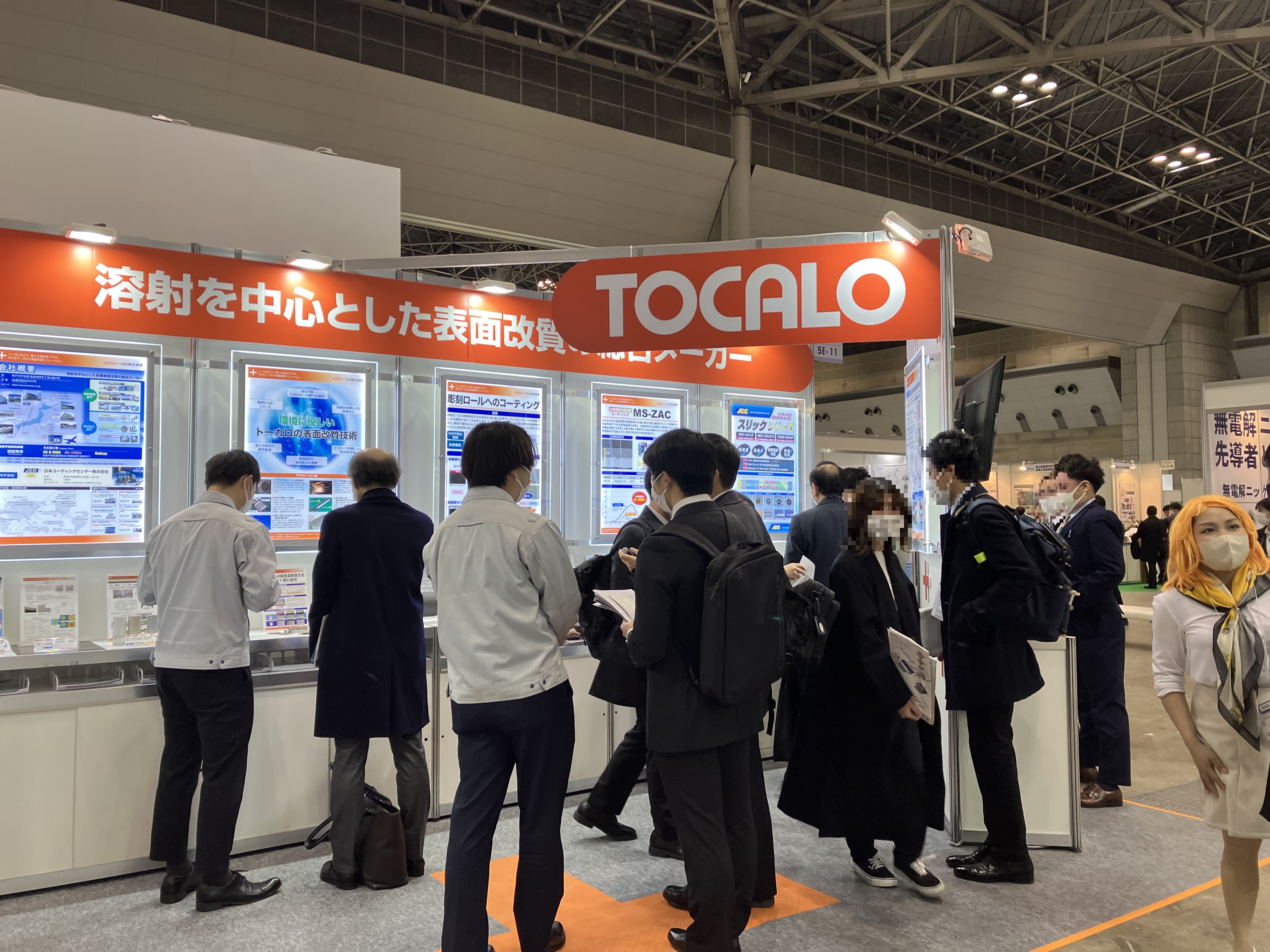
- September 2022: The International Industrial Fair Kobe 2022 (Kobe International Exhibition Hall)
- October 2022: Kansai Healthcare and Medical Equipment Development Exhibition 2022 (INTEX Osaka)
- October 2022: Automotive World Nagoya (Port Messe Nagoya)
- February 2023: 2nd Highly-functional Material Week (Makuhari Messe)
- February 2023: SURTECH2023 Surface Technology Element Exhibition (Tokyo Big Sight)
EMPLOYEE VOICES
Becoming a more preferred partner through rigorous customer orientation
Shu Adachi (Akashi Plant, Sales Division, Sales Department 1)
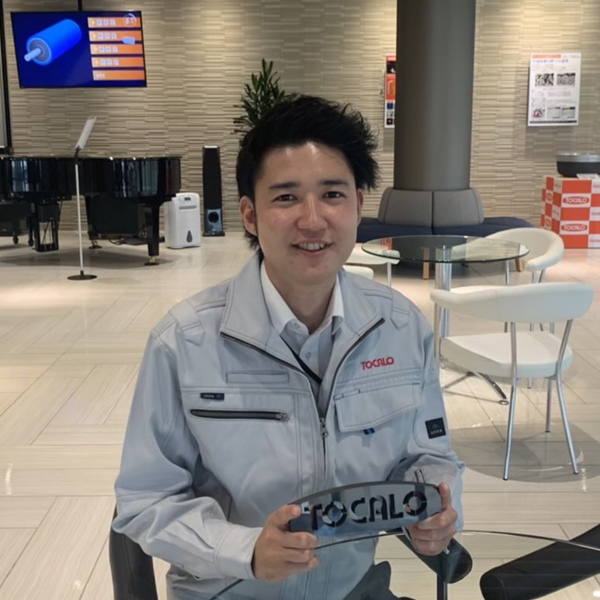
My role in the Sales Division is to handle steel manufacturers, and, as a sales representative, I am tasked with finding solutions to my customers' problems with TOKARO's surface treatment technology. In my work, the most important thing for me is to maintain a strong customer orientation, and therefore I am constantly thinking about what I can do to make the customer happy and be helpful to them. By putting myself in the customer's shoes, I can better understand their potential needs.
As part of our after-sales service, we perform regular inspections of surface-treated conveyor rollers every one to three months. Any abnormalities could cause an issue if left untreated, so we make sure to be diligent in our inspections and ensure our customers can enjoy stable operation.
I fondly remember an instance where we helped a customer avoid issues by discovering and rectifying an abnormality during one such inspection. At that time, the client said to us that we had been quite a bit of help in taking responsibility for after-sales service, implying that they would be relying on us going forward. It was then that I realized how important our popular after-sales services have been in our customers choosing TOCALO.
We believe that every problem that occurs with a customer's product for which we have performed surface treatment has a clue to its solution at the customer's site. For us, it is of great importance not only to win the trust of our customers but also to develop technologies through an accurate understanding of what kind of problems are occurring in actual operations involving our services. This is why we will continue to maintain a rigorous customer orientation in our field-first sales activities.
Quality Policy
TOCALO quickly formulates and submits product and service proposals using its surface modification technology to fulfill customer needs and continuously improve quality.
- Create products that fulfill customer quality requirement
- Clarify and strictly adhere to quality standards
- Set quality targets and evaluate degree of attainment
- Continuously improve the quality management system
Acquisition of ISO 9001 certification
All plants have acquired certification.
We continually improve our quality management system in order to improve customer satisfaction and earn social trust through quality assurance.
ISO 14001-certified plant | Registered date | Registration number | Certified activities |
---|---|---|---|
Kitakyushu Plant | Jul. 1998 | JQA-2470 | Thermal spray processing for industrial machinery parts, equipment parts for the chemical industry, and parts for FPD and semiconductor manufacturing equipment |
Tokyo Plant | May 1999 | JQA-QM 3344 | Surface treatment processing for industrial parts (thermal spray processing and other peripheral technologies) |
Akashi Plant | Oct. 1999 | JQA-QM 3810 | Surface treatment processing for industrial parts (thermal spray processing and other peripheral technologies) |
Kobe Plant | May 2003 | JQA-QMA 10001 | ZAC processing of parts for FPD and semiconductor manufacturing
equipment
TD processing of insert block molds for automobile forming mold |
Kurashiki Plant | Dec. 2011 | JQA-QMA 14492 | Surface treatment processing for industrial parts (thermal spray processing and other peripheral technologies) |
Nagoya Plant | Nov. 2017 | JQA-QMA15690 | Surface treatment of parts for general industrial and aerospace industries (thermal spraying) |
Process | Implementation items | Certified activities |
---|---|---|
Considering orders |
|
|
Process | Implementation items | Certified activities |
---|---|---|
Orders (processing instructions) |
Processing directives
|
|
Process | Implementation items | Certified activities |
---|---|---|
Manufacturing |
|
|
Process | Implementation items | Certified activities |
---|---|---|
Shipment |
|
|
Process | Implementation items | Certified activities |
---|---|---|
After-sales service |
|
|
Acquired JIS Q 9100, Nadcap certification (for the aerospace industry)
The Nagoya Plant has acquired certification for the aerospace industry.
JIS Q 9100 was established to manage the quality of aerospace defense products, which
requires advanced quality control. To satisfy requirements specific to the aerospace
industry, the Nagoya Plant acquired certification in November 2008. The Akashi Plant was
also certified in 2014, but the aircraft-related work was consolidated at the Nagoya Plant,
and the certification was returned at the end of March 2020.
Nadcap is an international
certification system under which the Performance Review Institute (PRI), an NPO in the
United States, reviews special process operations in the aerospace and defense industry.
ISO 14001-certified plant | Registered date | Registration number | Certified activities | |
---|---|---|---|---|
JIS Q 9100 | Nagoya Plant | Nov. 2008 | JQA-AS 0044 | Surface treatment of aerospace components (thermal spraying) |
Nadcap | Mar. 2014 | 9676204446 | Surface treatment of aerospace components (thermal spraying) |